News und Pressemitteilungen
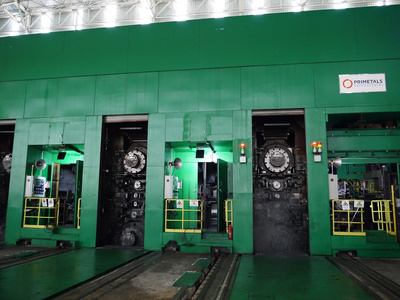
London, 23. Oktober 2017
Tosyali-Toyo startet die Blechproduktion in einem von Primetals Technologies gelieferten Kaltwalzkomplex
- Herstellung von kaltgewalzten verzinnten, feuerverzinkten und lackierten Blechen
- Produktionsbeginn markiert Tosyalis Expansion in den Flachproduktsektor
- Erstmaliger Einsatz des patentierten iBox-Beizprozesses in der Region Europa/MENA
Ein von Primetals Technologies gelieferter Kaltwalzkomplex hat am Produktionsstandort Osmaniye des türkischen Stahlerzeugers Tosyali-Toyo Celik A.Ş. den Betrieb aufgenommen. Der Kaltwalzkomplex besteht aus einer gekoppelten Beizlinie und Tandem-Kaltwalzstraße (PL-TCM), einer DurchlaufGlühlinie für verzinnte Stahlbleche (Tin-CAL) und einer Dressier-/DCR-(Double Cold Reduction)- Walzstraße (Temper/DCR). Die Anlage soll kaltgewalzte verzinnte, feuerverzinkte und lackierte Bleche erzeugen, die in erster Linie für Exportmärkte, aber auch für den Binnenmarkt vorgesehen sind. Damit expandiert Tosyali in den Flacherzeugnissektor. In der PL-TCM-Anlage kommt erstmals in der Region Europa/NEMA der patentierte iBox-Beizprozess zum Einsatz. Primetals Technologies hatte den Auftrag Ende 2014 erhalten.
Das im April 2012 gegründete Joint-Venture Tosyali-Toyo gehört zu 51 % dem türkischen Flach-, Langund Rohrprodukthersteller Tosyali Holdings und zu 49 % dem japanischen Stahlerzeuger Toyo Kohan. Für den neuen Produktionskomplex in Osmaniye wurde Primetals Technologies als Hauptauftragnehmer für die Lieferung der PL-TCM-, Tin-CAL- und DCR-Anlage ausgewählt. Der Auftrag umfasste die mechanische und elektrische technische Ausrüstung, die Automationssysteme sowie die Ingenieursdienstleistungen vor Ort, die Überwachung der Installation und Inbetriebnahme sowie die Schulung des Bedienpersonals.
Die PL-TCM-Anlage arbeitet mit dem patentierten iBox-Beizprozess und verwendet fünf SextoWalzgerüste in UCM-Bauform (Universal Crown Control Mill). Die Gerüste werden über eine volldigitale Drehstromsteuerung angetrieben und verfügen über die schnell ansprechende hydraulische Dickenregelung (HGC) Hyrop-F. Eine neue, hochmoderne automatische Dickenregelung (AGC) gewährleistet die Einhaltung der Dicke des gewalzten Bandes mit hoher Präzision. Die so ausgerüstete PL-TCM-Anlage ist für die Produktion von einer Million Tonnen hochwertiges Kaltwalzstahlband und Schwarzblech pro Jahr ausgelegt. Darüber hinaus steigert die Technologie die Herstellungseffizienz, verbessert die Ausbringung und Qualität der Produktion und ermöglicht auf diese Weise eine höhere Investitionsrentabilität. Die PL-TCM-Anlage verarbeitet Bandmaterial mit einer Einlaufdicke von 1,6 bis 4,0 mm. Die Auslaufdicke der Banderzeugnisse liegt zwischen 0,16 mm und 2,0 mm bei einer Breite von 700 bis 1.300 mm. Als maximale Bandgeschwindigkeit am Auslauf der Walzstraße werden 1.440 m/min erreicht. Es können die Sorten ULC (IF), HSLA und DD11-DD14 (DIN EN 10111) verarbeitet werden. Das maximale Coilgewicht beträgt 30 Tonnen.
Die Tin-CAL-Anlage hat eine jährliche Produktionskapazität von 240.000 Tonnen und dient zur Weiterverarbeitung des von der PL-TCM-Anlage erzeugten Bandmaterials mit einer maximalen Banddicke von 0,8 mm. Der Vertikal-Glühofen besteht aus Abschnitten zum Vorwärmen (PHS), Anwärmen (HS) und Durchwärmen (SS) sowie aus drei Kühlabschnitten (1CS, 2CS, 3CS) und wurde vollständig von Primetals Technologies entwickelt. Der Glühofen ist für die flexible Herstellung aller Behandlungszustände T1 bis T5 ausgelegt. Hinter dem Reinigungsabschnitt befindet sich ein kompaktes Streckrichtgerüst zum Ausgleich von Formabweichungen des Bandmaterials. Dies ist wichtig, um einen reibungslosen, zuverlässigen Betrieb des Glühofens auch bei der maximalen Bandgeschwindigkeit von 500 m/min zu gewährleisten.
Die Dressierstraße (Temper-DCR) hat eine jährliche Produktionskapazität von 303.000 Tonnen bei einer maximalen Liniengeschwindigkeit von 1.500 m/min. Ihre zwei UCM-Gerüste können wahlweise eine doppelte Kaltreduktion (DCR) oder einen Nachwalzprozess in zwei Gerüsten durchführen. Beim DCRProzess wird das geglühte Band nach der Reduktion in einer Tandem-Kaltwalzstraße im Walzgerüst Nr. 1 reduziert und in Gerüst Nr. 2 nachgewalzt und erhält dadurch seine geforderte mechanische Festigkeit. Beim Nachwalzen mit zwei Gerüsten wird das Band in den beiden Gerüsten Nr. 1 und Nr. 2 auf das vorgeschriebene Längungsverhältnis gewalzt, um die gewünschten mechanischen Eigenschaften zu erzielen. Wie die Tin-CAL-Linie verarbeitet auch diese Walzstraße Bandmaterial aus der PL-TCM-Anlage. Zum Nachwalzen kann die Einlaufdicke des Bandmaterials 0,16 bis 1,2 mm betragen, für den DCR-Prozess 0,18 bis 0,4 mm. Die Auslaufdicke des DCR-gewalzten Bandes kann zwischen 0,12 und 0,3 mm liegen. Zulässige Stahlsorten sind T1 bis T5 und DR6 bis DR10.
Sexto-UCM-Walzgerüst (Universal Crown Control Mill) von Primetals Technologies im Anlagenkomplex von Tosyali-Toyo Celik A.Ş. in Osmaniye, Türkei.
Primetals Technologies, Limited mit Sitz in London (Großbritannien) ist ein weltweit führender Partner für Engineering, Anlagenbau und Lifecycle-Services in der Metallindustrie. Das komplette Technologie-, Produkt- und Leistungsportfolio des Unternehmens umfasst ganzheitliche Lösungen für Elektrik, Automatisierung und Umwelttechnik und deckt alle Schritte der Wertschöpfungskette in der Eisen- und Stahlproduktion vom Rohstoff bis zum fertigen Produkt ab sowie modernste Walzwerkslösungen für NE-Metalle. Primetals Technologies ist ein Joint Venture von Mitsubishi Heavy Industries (MHI) und Siemens. Das bei MHI konsolidierte Unternehmen Mitsubishi-Hitachi Metals Machinery (MHMM) mit Beteiligungen von Hitachi, Ltd. und der IHI Corporation hält 51 % der Anteile und Siemens 49 % der Anteile an dem Joint Venture. Das Unternehmen beschäftigt weltweit etwa 7.000 Mitarbeiter. Weitere Informationen sind im Internet verfügbar unter www.primetals.com