News & Press Releases
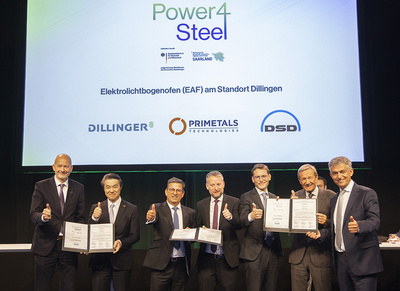
London, October 11, 2024
Dillinger and ROGESA Choose Primetals Technologies as Supplier for Major Decarbonization Project
- Primetals Technologies to supply and implement DRI plant and EAF Ultimate
- New green steel production complex with an annual capacity of 2 million tons
- DRI plant to be provided in collaboration with Midrex Technologies
- Represents significant step in Dillinger’s and ROGESA’s conversion to decarbonized production
On October 11, German steel producer Dillinger and its subsidiary ROGESA signed contracts with Primetals Technologies for the supply of a new production complex, which includes a DRI plant, contracted along with Midrex Technologies, and an EAF Ultimate electric arc furnace plant including two twin ladle furnaces. These solutions from Primetals Technologies will support Dillinger and ROGESA to meet their goal of reducing CO2 emissions by 4.8 million tons per year within six years.
Dillinger and ROGESA, as part of the SHS Group (SHS – Stahl-Holding-Saar), have launched an ambitious green steel transformation project to replace the current blast furnace-based production route in Dillingen, Germany. Having a single supplier for the complete range of ironmaking and steelmaking facilities comes with several benefits for Dillinger and ROGESA, particularly in terms of implementation and tailored design features to accommodate for plant installations alongside existing equipment. Dillinger and ROGESA chose Primetals Technologies based on its leading technological solutions and strong references for both DRI plants and EAF technology.
“This partnership with Primetals Technologies represents an important building block on the way to climate friendly steel production here in Germany, “ said Dr. Peter Maagh, Chief Technical Officer at Dillinger. “We are convinced that we can successfully launch our Power4Steel decarbonization project on schedule with such an experienced and reliable partner.“
DRI Plant for Flexible Transition to Hydrogen
The new direct reduction plant will produce hot direct reduced iron (HDRI) and cold DRI (CDRI) with an annual capacity of 2 million tons. A consortium of Midrex and Primetals Technologies will handle the engineering and supply of both mechanical as well as electrics and automation equipment. This includes a material handling system, a water treatment plant, auxiliary equipment, and training and advisory services. Primetals Technologies will also provide a complete basic (Level 1) and process optimization (Level 2) system featuring the DRIpax expert system, which ensures consistent high quality of the produced DRI.
“The transition to green steel production will not happen overnight, we will see a step-by-step process towards carbon neutrality,” said Andreas Viehböck, Head of Upstream Technologies at Primetals Technologies. “With this investment, Dillinger and ROGESA are set to reach their mid- to long term goals in terms of decarbonization. The solutions from Primetals Technologies and Midrex will allow them to ramp up the use of hydrogen gradually while adapting to a changing energy landscape. We are very happy to support them on this endeavour and beyond.”
The MIDREX Flex technology is designed to operate at different ratios of natural gas and hydrogen, up to 100 percent hydrogen. Initially, the plant will be operated with a mix of natural gas and hydrogen, allowing for a carbon footprint reduction of more than 50 percent compared to blast furnace based ironmaking. The MIDREX Flex plant will be implemented with hydrogen-ready equipment and piping, such as three stages of process gas compressors. Moreover, it features a hot transport conveyor to utilize the valuable heat of the HDRI for direct charging into the electric arc furnace at the Dillingen site. A DRI cooling solution will enable the transport of CDRI.
“The decision by Dillinger and ROGESA for MIDREX Flex technology allows them to transition to hydrogen-based ironmaking at the pace that matches the availability of sufficient gas supply while reducing their current CO2 emissions significantly,” K.C. Woody, Midrex President and CEO, said. “DRI-based steelmaking provides a pathway to a sustainable future, both economically and environmentally, and our technology solutions offer the flexibility and performance to turn promise into success.”
EAF Ultimate – High Flexibility and Fully Automated Operation
The EAF Ultimate represents Primetals Technologies’ latest development in electric steelmaking. The fully automated plant will ensure short tap-to-tap times and reduced consumption. It offers high flexibility in terms of raw material input and the production of a wide range of steel grades.
Primetals Technologies extensive scope of supply for the new meltshop includes a 195-ton furnace with a 9.6-meter furnace diameter and a powerful 300 megavolt-amperes (MVA) transformer, the LiquiRob robotics system for enhanced safety operations, two 195-ton twin ladle furnaces (LF), a material handling system, primary, secondary, and auxiliary dedusting systems for the EAF plant, a waste heat recovery system, and a water treatment plant. The heat recovery system converts waste heat into steam, which will be reused in other production units.
The EAF Ultimate will feature advanced Level 1 and Level 2 automation systems, including the EAF Controller and EAF Optimizer, enabling both closed-loop control of the furnace for a precise fulfilment of the desired product quality and detailed production planning.
Comprehensive Digitalization Solutions
A swift implementation of learnings and evaluations will play a key role as the new production complex is put into operation, which places high demands on the automation systems. Both plants will be equipped with the latest digitalization solutions from Primetals Technologies. The condition-monitoring system Asset Life Expert (ALEX) identify potential incidents before they occur to support predictive maintenance, which together with the Lomas off-gas analysis system will enhance process-efficiency and safety.
Primetals Technologies’ virtual plant solutions for both the DRI and the EAF plant will allow testing of software and operator training before startup and throughout the entire lifecycle of the plant, ensuring a smooth ramp-up of production. Moreover, the scrap yard will be equipped with AI-based sensor systems, allowing fully automated operation of the scrap yard.
The Melt Expert electrode control system will be installed at both the EAF plant and the LFs, offering productivity gains and cost-savings related to reduced consumption.
Leading Supplier of Decarbonization Technologies
Primetals Technologies and its consortium partner DSD Montagetechnik, part of the German DSD Steel Group, will provide advisory services for the construction and implementation of the DRI plant and EAF equipment.
Dillinger and ROGESA’s new production complex is Primetals Technologies’ latest major decarbonization project. Recently, Oslo-based Blastr selected the company as its technology partner for new green steel production facilities in Finland. This, along with projects for voestalpine in Austria, Salzgitter in Germany, and Marcegaglia in the UK for comprehensive EAF projects, solidifies Primetals Technologies’ role as leading supplier of decarbonization solutions.
Carbon Neutrality by 2045
SHS Group, consisting of several leading companies in the steel market, aims to achieve carbon neutrality by 2045 through its ambitious Power4Steel program. Steel products from SHS Group companies are used in demanding applications, such as the headquarters of French daily newspaper Le Monde and London’s tallest building, Twentytwo, as well as in the safe tracks of European high-speed trains and in the majority of cars manufactured in Europe.
SHS Group has obtained funding for its green transition from the German state and the state of Saarland. The fundings are approved by the European Union.
Dillinger and ROGESA have chosen Primetals Technologies as supplier of a new production complex, which marks a significant step in the green transition of its production process in Dillingen, Germany.
The DRI plant will be provided by a consortium of Midrex and Primetals Technologies.
EAF Ultimate electric arc furnace plant from Primetals Technologies.
Primetals Technologies, Limited, headquartered in London, United Kingdom, is a pioneer and world leader in the fields of engineering, plant building, and the provision of lifecycle services for the metals industry. The company offers a complete technology, product, and services portfolio that includes integrated electrics and automation, digitalization, and environmental solutions. This covers every step of the iron and steel production chain—from the raw materials to the finished product—and includes the latest rolling solutions for the nonferrous metals sector. Primetals Technologies is a Group Company of Mitsubishi Heavy Industries, with around 7,000 employees worldwide. To learn more about Primetals Technologies, visit the company website www.primetals.com.