COPPER/COPPER ALLOY COLD AND FOIL ROLLING MILL
The most advanced copper and copper alloy rolling mills in the world enable producers to achieve the highest quality and quantities.
Primetals Technologies offers solutions that satisfy increasing market demand for and trends toward rolled copper and copper alloy sheet/foil. The appropriate mill configuration is crucial for meeting various quality, productivity, and characteristic requirements. Primetals Technologies’ extensive portfolio includes the cluster type mill (6/10-high, 12-high, 20-high), 4-high conventional mill, and 6-high Universal Crown Control Mill (UC-MILL), meeting any customer requirement, and enabling the effective production of high-quality sheet/foil to tight tolerance requirements.
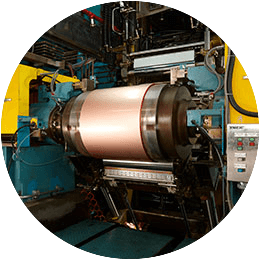
Excellent shape control and high productivity
UC-Mill
The UC-MILL for copper and copper alloys features small work rolls (WR) combined with shape control functions consisting of WR bending, intermediate roll (IMR) bending, IMR shift using all straight uncambered rolls, and a spot cooling system. The UC-MILL enables the rolling of hard and thin material with excellent shape control. Furthermore, equipped with a cobble guard and air wiping system at the mill exit, side and good wiping ability can be achieved during high-speed rolling.
X-Mill
The X-Mill with intelligent shape control is designed for ultra-thin foil rolling. The rolls are arranged in an X configuration in which a pair of parallel back-up rolls support each side of the small diameter work rolls at a tangent below the WR top to prevent horizontal deflection. This enables stable and reliable thin-gauge rolling to be performed.
Features:
- Compact and simple mill arrangement
- Optimized mill size and layout
- Stable rolling
- Automatic mill set-up
- High speed rolling
- Minimal downtime
- Quality product
Want to know more? Go to Lifecycle Services & Integrated Plants & Solutions
Complete automation and process control for Aluminum Cold Rolling Mills
Plant productivity and product quality are governed to a large extent by the quality of plant automation, process control, and available process optimization functions.
- Digitalization packages (e.g. TPO, MAT, Condition Monitoring, Intelligent Sensors)
- Production management systems (Level 3)
- Physical models combined with artificial intelligence (Level 2)
- Automation solutions, including advanced technological controls (Level 1)
For existing installations optimization packages are available as standalone solutions designed to improve production efficiency and strip quality.
Throughput maximization with:
- Production Optimization Modes
- Mill Set-Up System (MSU) as alternative to a model-based Level 2 system, including user-friendly pass schedule strorage and mathematical calculations
Excellent strip quality with:
- Automatic Gauge Control (AGC)
- Flatness Expert - Model-based Automatic Flatness control
- Roll Eccentricity Expert for uniform and accurate strip thickness
- Coil Eccentricity Expert for uniform and accurate strip thickness
Our solutions encompass:
- Process Automation Twin for safely developing new materials and optimizing rolling schedules
- Central Operation Cockpit to support mill operation (centralized operation)
- Software architecture open for customers' own future developments
- Modular structure for step-by-step modernizations
TECHNOLOGY AND MODERNIZATION PACKAGES
Get striking results with incremental investments
Name | Short Description |
---|
Name | Short Description |
---|
Name | Short Description |
---|---|
Integrated Solenoid Valve (ISV) Spray System | ISV Roll coolant spray bars for hot and cold rolling mill strip flatness control |
Position Transducer | Position measurement of rolling mill hydraulic capsule |
Air Bearing Shapemeter | Shape measurement of rolled metal sheet and foil |
Modular Coil Shuttle System (MCS) | Rail-based, fully automated modular coil transport system |
Reference Story: High-productivity copper/copper alloy rolling mill
Customer:
Chinalco Shanghai Copper, China
Type of Plant:
Reversing Foil Mill for ultra-thin copper foil.
Our Solution:
This X mill with Air Bearing Shape Meter (ABSM) and hot spot spray is first application in China. 6-micron thickness was achived early in the commissioning stage. This is the first copper foil mill to start commmercial production with 10 microns or less in China.