CUTTING-EDGE TECHNOLOGIES FOR IRONMAKING — GREENER THAN EVER BEFORE
Primetals Technologies provides technological solutions along the entire value chain of ironmaking and metallurgical automation solutions.
Global demand for iron and steel is constantly rising. At the same time, sourcing high-quality raw materials and satisfying energy needs can be a challenge. In this dynamic environment, steel plants have to utilize all available technologies to become greener and more environment friendly, and to improve their ecological footprint especially in terms of CO2 emissions.
Our focus is on you – with your unique goals and requirements. Primetals Technologies combines expertise in plant design and construction with great competence regarding the optimization of the steel-production process. Our pioneering research and development efforts extend to groundbreaking hydrogen-based direct-reduction solutions.
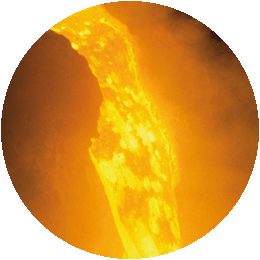
MIDREX® — THE WORLD’S LEADING DRI PRODUCTION PROCESS
MIDREX is an innovative ironmaking process that has been specifically developed to produce direct – reduced iron from iron ores and natural gas/hydrogen.
MIDREX is a gas-based shaft furnace process that converts iron oxides – in the form of pellets or lump ore – into direct-reduced iron (DRI). MIDREX technology is highly customizable, which means it can be tailored to each customer’s specific needs, and this is reflected in a wide variety of configurations. The performance of MIDREX plants typically exceeds nominal capacity ratings. This trend will continue with the implementation of new technologies such as process water degassing, hydrogen utilization, seal gas dry de-dusting system, slurry treatment, and the new and successful DRIpax process optimization system.
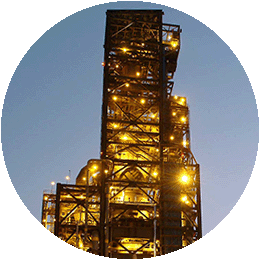
BLAST FURNACE TECHNOLOGIES – INNOVATION AND INCREMENTAL DECARBONISATION
Meeting the twin demands of extending blast furnace life and reducing CO2 emissions
Primetals Technologies has provided blast furnace engineering, project excellence and expertise world-wide for over a century. Our technologies cover the entire blast furnace process route from raw materials to clean gas and hot metal / slag processing. Our capabilities include feasibility and process studies, a wide range of technical products and solutions, environmental, CO2 and energy saving answers, automation systems, and the ability to execute the full range of project models. This capability forms the basis for successful project completion and start-up, for the complete range of solutions from small to ultra-large blast furnaces.
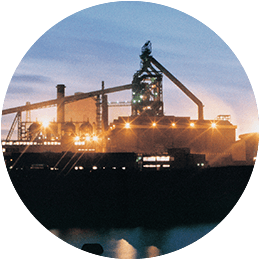
FINEX® — INNOVATIVE AND ENVIRONMENTALLY FRIENDLY IRONMAKING
Finex is an innovative ironmaking process based on the direct use of fine ore and non-coking coal.
In the Finex process, fine iron ore is directly charged at the top of a cascade of fluidized-bed reactors, where it is heated and reduced to direct-reduced iron (DRI) by means of a reduction gas derived from the gasification of the coal in the melter gasifier. The DRI fines are processed into hot-compacted iron, transferred in hot condition to a charging bin positioned above the melter gasifier, and then charged into the melter gasifier, where melting takes place. The tapped product – liquid hot metal is equivalent in quality to the hot metal produced in a blast furnace or Corex plant.
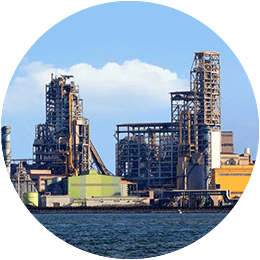
COREX® — COST-EFFICIENT AND ENVIRONMENTALLY FRIENDLY IRONMAKING
Corex, the unique smelting-reduction process allows for the cost-effective and environmentally friendly production of hot metal from iron ore and coal.
In the Corex process, all metallurgical work is carried out in two separate process reactors – the reduction shaft and the melter gasifier. Because coking and sintering plants are not required, and a lower-cost coal compared to the blast furnace route can be used, substantial cost savings of up to 20% can be achieved in the production of hot metal. Corex plant emissions contain only insignificant amounts of NOx, SO2, dust, phenols, sulfides, and ammonia, so emission values come in below the maximum values permitted by European standards. Furthermore, waste-water emissions are far lower compared with the conventional blast furnace route.
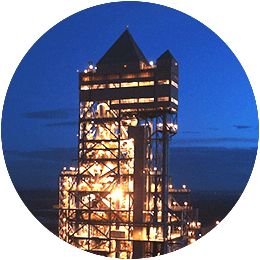