METALLIC COATING LINES — ADDING VALUE FOR A WIDE RANGE OF APPLICATIONS
A major trend in the steel industry is increasing added-value and profit margin on rolled product through the application of metal coatings.
A broad range of solutions is offered for metallic coating of both hot-rolled and cold-rolled strip in continuous hot-dip coating lines. This value-added, high-quality material is extensively used in construction, in appliances, in automotive and in packaging applications as a well-proven and time-tested solution for corrosion protection.
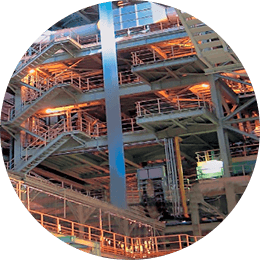
CONTINUOUS GALVANIZING AND OTHER METALLIC COATING LINES
To meet both your expectations and your market requirements (steel grades, gauges, coatings, quality, etc.), Primetals Technologies designs and implements different solutions according to your upstream production facilities and process route.
Based on the above considerations and additional customer constraints, the most suitable solution will be proposed.
Various combinations of processes (combi-lines) can also be proposed to optimize your production routes and costs in the field of hot-dip coating (True Zinc, Galvanneal, Aluminum Zinc, Zinc Magnesium, and Aluminum coatings):
- Continuous Galvanizing Lines (CGL)
- Continuous Annealing or Galvanizing Lines (CAGL)
- Combined Continuous Galvanizing and then Color Coating / Painting Lines (CGPL, GPL)
- Combined Continuous Pickling and then Galvanizing Lines (CPGL, PGL)
Main Benefits
- Numerous references and many years of experience
- Overall responsibility, capability and global expertise
- Internal solutions for Mechanical, Furnace, Automation, and In-house mechatronic machines
Furnace and cooling section
- Flexibility to produce the most advanced steel grades in the industry, including exposed automotive and 3rd generation AHSS
- High-efficiency, direct fired furnace (DFF) utilizing proprietary MID Burners provides direct flame, convective impingement
- Improved wettability of higher alloy substrates, including oxidizing DFF burners, separate strip pass oxidation chamber, and dewpoint control in radiant tube furnace (RTF)
- Transverse flux induction system enables higher temperature thermal cycles, reduces radiant tube furnace load, and eases transition control
- Patented high hydrogen, rapid cooling achieves 150C/sec/mm utilizing patent-pending T-nozzle plenums ensuring uniform temperature profile across the strip width
- FLEXIT equalize section allows for greater flexibility to produce complex thermal cycles utilizing accurate temperature control with advanced thermal models
Mechatronic machines for Metallic Coating Lines
In-house mechatronic machines designed, assembled and tested in our Primetals Technologies workshops:
- Horizontal furnace and vertical furnace
- Robot solutions for dross management
- Automatic ingot charger
- Skin-Pass Mill, Tension Leveler, Scale Breaker (more than 400 references worldwide)
- PropertyMon Inline Mechanical properties gauge
- Turret-type Side Trimmer, EdgeMon® (edge monitoring), and Scrap Chopper
Want to know more? Go to Lifecycle Services & Integrated Plants & Solutions
Complete automation and process control for Metallic Coating Lines
With its automation solutions, Primetals Technologies offers optimum process control and throughput optimization. This is reflected in the 79 references for coating lines Primetals Technologies has supplied worldwide in the last 15 years. Our focus is on the continuous improvement of the following requirements.
Throughput Optimization
- Flexible coil schedule and coil split function
- Intelligent looper filling strategy
- Cutting program optimization
- Speed Optimization System
Inline Process Quality Insurances
- Strip defects follow-up with preventive defects passing strategy
- Transparent cleaning process monitoring and control
- Stable process tension control with load shearing
- Balanced roughness and elongation control in skin pass mill
- Closed loop flatness control
- Automatic Coiling tension distribution
Final Product Quality Certification
- Process data recording
- Product classification report
Production and Plant Condition Monitoring
- Process equipment condition monitoring
- Bridle slippage detection and preventive control
- High accuracy flying shear control
TECHNOLOGY AND MODERNIZATION PACKAGES
Get striking results with incremental investments
Name | Short Description |
---|
Name | Short Description |
---|
Name | Short Description |
---|
Name | Short Description |
---|---|
EdgeMon | Inspection of side-trimmed strip edge surface for steel pickling and processing lines and aluminum rolling |
Flying Width Changing (FWC) side trimmer | Innovative solution for efficient and accurate side trimming |
Name | Short Description |
---|
Name | Short Description |
---|
Reference Story: Optimized production of construction material
Customer
Maruichi Sun Steel Joint Stock Company (SUNSCO), Vietnam
Type of plant
Continuous Galvanizing Line
Technical Data
Annual capacity: 280,000 tons
Strip thickness: 0.3 – 3.2 mm
Exit Strip width: 700 - 1250 mm
Center Speed (Max):120 m/min
Our solution
This CGL with the following benefits is fully appreciated in South East Asia:
- Galvanized steel of GI and GL for construction material can be produced from both Hot and Cold band material
- Alkali cleaning system at furnace entry, Skin Pass Mill and Tension Leveler after Pot are equipped for improvement of strip quality and surface shape even though Horizontal furnace
- Roll coater at chemical treatment section and Electrostatic Oiler at delivery section realize uniform surface coating
- Two tension real system can realize small lot production