News & Press Releases
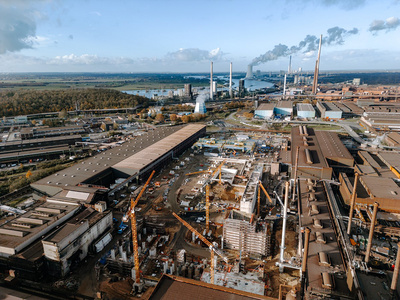
London, December 11, 2023
Construction Work for Slab Caster and Hot-Strip Mill to Begin at thyssenkrupp Steel in Duisburg
- Major upgrade project enables manufacture of high-strength steel grades and adaptation of production to both current and future needs
- Continuous slab caster featuring a wide range of advanced Level 2 automation systemsensures an optimized casting process
- Modernized hot-strip mill with intelligent assistant systems for faster and stable rolling of steel strip
thyssenkrupp Steel has reached an important milestone in the major slab caster and hot-strip mill project at its Bruckhausen site in Duisburg, Germany, as the steel giant recently held a cornerstone ceremony that marked the start of on-site pre-assembly work for both continuous caster No. 4 and hot-strip mill No. 4. The ceremony took place just days after the inauguration event for the 2-stand reversing cold mill, supplied by Primetals Technologies, at thyssenkrupp Steel’s Bochum site.
“Our new and rebuilt facilities will enable us to meet the changing needs of the market, e.g. the demand for higher strength steel grades, lower tolerances, and optimized surfaces,” said Heike Denecke-Arnold, Chief Operations Officer at thyssenkrupp Steel. “This is also a strong signal to our customers, who will benefit from increased flexibility and availability, as a result of the new facilities.”
“We are very happy to collaborate with thyssenkrupp Steel in this massively important project that will have a great impact not just in the Rhine and Ruhr region in Germany but also for Europe as a whole. Close to a third of the larger investment plan comes from Primetals Technologies, and our technology will ensure that thyssenkrupp steel is set to supply the fast-growing markets for high-strength steel and other advanced steel grades,” said Hans-Jürgen Zeiher, Head of Electrics and Automation at Primetals Technologies.
In 2021, thyssenkrupp Steel placed a major order with Primetals Technologies for a reversing cold mill, the hot-strip mill, and two thick-slab continuous casters. Together, these upgrades are centerpieces in thyssenkrupp’s plans, and all the projects are scheduled to be completed over the course of 2025.
The project at the Bruckhausen site will separate the existing casting and rolling line into a revamped caster and a modernized hot-strip mill. The existing integrated mill can no longer meet the demanding needs of the automotive industry as well as other rapidly growing markets. Separating the casting and rolling sections will ensure highly effective production of high-strength steel grades and premium end products.
Advanced casting solutions
The revamped 2-strand continuous caster No. 4 will feature advanced and comprehensive mechanical and automation solutions. A mold-width adjustment system, DynaWidth, is used to enable agile and fast slab-width changes. The DynaFlex hydraulic oscillator flexibly adjusts the mold-oscillation parameters, resulting in improved strand-surface quality of the slabs. The Level 2 automation system features a wide range of modules, including Dynacs 3D, a model that ensures optimal adjustment of secondary-cooling setpoints, DynaGap SoftReduction 3D, a fully automatic roll-gap control system for improved metallurgical properties of the strand, and Mold Expert technology for early detection of caster-mold breakouts, which results in increased plant availability.
The new 2-strand continuous caster No. 3 will replace the existing caster No. 1 at the Bruckhausen plant once the revamp of the casting-rolling line is completed.
Modernized hot-strip mill
There will be numerous benefits for thyssenkrupp Steel stemming from the modernized hot-strip mill. Fewer edge cracks and reduced material waste will result in improved yield, and the product portfolio will be extended with, for example, high-strength steels as well as grades for the e-mobility industry. The widened product scope is realized mainly thanks to the patented Encopanels, a heat retention system that reradiates heat back into the transfer bar, and increased rolling and bending force at the finishing mill.
Featuring energy-efficient solutions, both new and proven, the single stand 4-high reversing roughing mill will be installed right after the new caster No. 4 and the two new walking beam reheat furnaces. In addition, the first two finishing mill stands and the strip cooling system will be upgraded. Primetals Technologies will also supply comprehensive Level 1 and 2 automation systems and provide advisory services for installation and start-up.
The automation systems represent state-of-the art technology. Intelligent assistant systems stabilize the strip when being processed in the rolling mill. The production remains stable even during changes of process conditions, for instance when operators initiate a speed change. This is mainly thanks to a consistent temperature control function and an advanced contour control system across the entire roughing and finishing line – both modules are part of the Level 2 automation system.
With an annual production volume of around 11 million tons of crude steel, thyssenkrupp Steel employs around 26,000 people across the world. thyssenkrupp Steel has set itself the goal of producing five million tons of CO2-neutral steel annually by 2030. By 2045 at the latest, the German steel producer wants all production to be climate neutral.
With the laying of the cornerstone for the construction of a modern hot-strip mill, the conversion and construction of two continuous casting plants, and the construction of two new walking beam furnaces, thyssenkrupp Steel is taking decisive steps to strengthen its position in European competition. Photo copyright: thyssenkrupp Steel.
Representatives from thyssenkrupp Steel and Primetals Technologies during the ceremony. From left to right: Harald Espenhahn, Head of Technology & Environment at thyssenkrupp Steel, Hans-Jürgen Zeiher, Head of Electrics and Automation, Olaf Meininghaus, Corporate Account Manager, both with Primetals Technologies, Andy Rohe, Head of Downstream Operations, and Chris Lindner, Head of Upstream Operations, both with thyssenkrupp Steel. Photo copyright: thyssenkrupp Steel.
Primetals Technologies, Limited, headquartered in London, United Kingdom, is a pioneer and world leader in the fields of engineering, plant building, and the provision of lifecycle services for the metals industry. The company offers a complete technology, product, and services portfolio that includes integrated electrics and automation, digitalization, and environmental solutions. This covers every step of the iron and steel production chain—from the raw materials to the finished product—and includes the latest rolling solutions for the nonferrous metals sector. Primetals Technologies is a Group Company of Mitsubishi Heavy Industries, with around 7,000 employees worldwide. To learn more about Primetals Technologies, visit the company website www.primetals.com.