CO2 Emission and Cost Optimization of Steelworks
Pressure is mounting on steel producers to optimize CO2 emissions and keep operating costs under control. Beside nominal operation also the effects of idling-maintained plants in terms of cost, CO2 emissions, mass and energy flows are of key interest. In this webinar, we will show you how we use a single tool to represent, simulate, and then optimize the entire production – even under changing conditions – of steelworks, providing a reliable means of planning and an effective way to cut costs.
Focusing on best-practice examples for the optimization of a plant, we will demonstrate how to use offline simulations to optimize costs, CO2 emissions and energy distribution – reacting to changes in raw materials and their quality or short-term changes in steelworks configuration due to maintenance work.
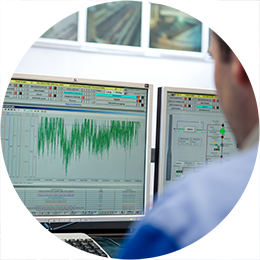
Target audience:
- Technology departments
- Strategic planning or controlling departments
- Raw material purchasing department
- Management
- Operation decision makers
- Investment department
- Plant Managers
Key takeaways:
- Learn how voestalpine solved their requirement for strategic operation planning at gowest Texas
- Learn for which applications in an integrated steel plant the simulation tool m.simtop provides optimal assistance for decision makers, management and operation planers
- Learn what challenges and hurdles have to be overcome
- Experience a live demonstration of m.simtop “in action”
SPEAKERS
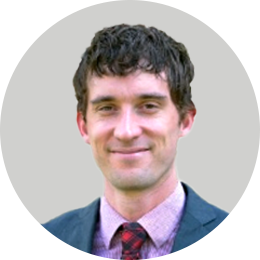
CHRISTOPHER HARRIS
Senior Research Engineer, Voestalpine
Chris Harris received his Bachelor of Engineering and Doctorate in the area of extractive metallurgy. Chris began his career as a metallurgical consultant working in the areas of technology development, plant design and plant optimization and de-bottlenecking. After 6 years as a technical consultant, Chris joined voestalpine in 2016 to help with the commissioning and ramp-up of voestalpine’s HBI plant in Texas. Chris currently works in the central R&D group of voestalpine, where he is responsible for ongoing R&D activities for the voestalpine Texas plant, and is part of a team examining low CO2 steel production routes for the voestalpine Steel Division.
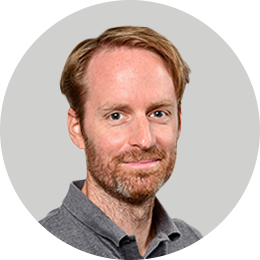
BERND WEISS
Senior Expert Process Simulation Technologies, Primetals Technologies
Bernd Weiss has over 12 years of experience in the ironmaking industry after graduating as a chemical engineer at TU Vienna. His experience covers being process engineer for COREX, MIDREX and FINEX, process safety coordinator as well as R+D project leader. His career also embraced several stays for plant start-ups abroad. Since 2010 he started the m.simtop metallurgical process simulation platform development. Today, as senior process simulation expert, he coordinates the steadily competence extensions of m.simtop together with strategic partners.
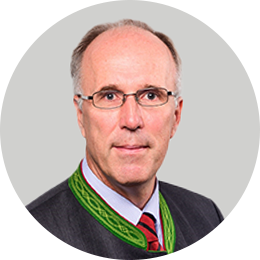
CHRISTIAN BÖHM
Head of Sales - Direct Reduction Plants, Primetals Technologies
Christian Böhm has over 30 years of experience in the ironmaking industry. After graduating as a metallurgical engineer from the Montanuniversität Leoben in Austria, he joined Primetals Technologies in the ironmaking department for the COREX and FINEX Process when these processes were still in their infancy. Later-on he managed COREX and FINEX and other ironmaking projects and became head of sale of smelting and direct reduction plants which also includes the MIDREX Process. Being part of several committees of the IEA, VDEh, IIMA and other organizations, he tries to contribute with his knowledge and experience to the benefit of the iron and steel industry.