News & Press Releases
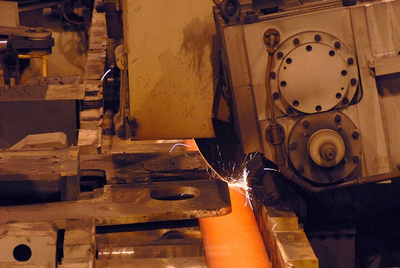
London, August 01, 2017
Primetals Technologies receives additional modernization order for Çemtaş bar rolling mill in Turkey
- New equipment improves productivity and yield
- Hot dividing shear allows the use of the longer 200 mm billets in production.
- Abrasive disk saw is able to cut wider layers of bars
- Automatic bundling and packing system replaces a manually operated system
Turkish steel producer Çelik Makina Sanayi ve Ticaret A.Ş. (Çemtaş) has awarded Primetals Technologies another order to modernize its bar rolling mill in Bursa. The rolling mill will be equipped with new dividing and handling systems. The new hot dividing shear allows the use of the longer 200 mm billets in production, the new abrasive disk saw is able to cut wider layers of bars and a new automatic bundling and packing system replaces a manually operated system. With these measures, existing systems can be used more efficiently and current productivity limitations can be overcome. The modernization is due to be finished in the fourth quarter of 2017.
This current project is part of the second phase of an overall plan for mill modernization, which included the supply of a reversing sliding roughing stand and an intermediate train by Primetals Technologies as well as the modernization of the existing finishing. This first phase was successfully concluded with the reception of the FAC in October 2016. Also, Primetals Technologies is currently modernizing an electric arc furnace at the Bursa plant. The new equipment will shorten the melting time and reduce the consumption of electrodes, electricity, oxygen and carbon.
Primetals Technologies is responsible for the engineering of the complete process equipment, the design of the supplied equipment as well as for advisory services to erection, startup, commissioning and training. The scope of supply also includes main and auxiliary drives and motors, the basic automation (level 1) and interface with existing mill automation and the mechatronical packages for the new equipment.
The new hot dividing shear for rounds and flats replaces an existing shear and has a higher cutting capacity. It allows the use of longer 200 mm billets in production.This way, the reheating furnace can be used at higher production potentiality. This will increase the final yield of the rolled products. The shear has a direct type drive which starts and stops every cutting operation and features low maintenance requirements due to simple its mechanical arrangement. It also allows for high and repeatable cutting accuracy for increased yield. Reduced cycle times results in easier setting of cooling bed lengths.
The new abrasive disk saw is also designed for both rounds and flats. While the existing saw is using a maximal diameter of 850 mm disks and can cut a layer of maximum 750 mm, while the existing roller table barrel length already accomodates layers up to 1,000 mm. The abrasive saw has a maximum diameter of 1,250 mm and is able to use the whole roller table length in order to cut a maximum layer 1,000 mm of bars. This overcomes the present productivity limits.
An automatic bundling and packing device for flats and rounds will be installed to replace the second manual packing device in Hall A of the plant. An H/V roller table downstream the automatic stacker will transfer the pack to the binding area, which will be equipped with two automatic strapping machines and a wire binding machine. The stacking system is capable to handle also flat bars, so that they can be orderly piled in a stack with a neat shape that allows easy and quick storage/handling operations.
Çemtaş had placed a first modernization order of bar rolling mill with Primetals Technologies in early 2014. The mill is designed to produce 200,000 metric tons of long products per year, including rounds with diameter from 15 to 100 mm and flat bars with thicknesses ranging from 5.5 to 62 mm at widths between 46 and 140 mm. Steel grades encompass spring, high and low carbon, case hardening heat treatable grades as well as HSLA (high-strength low-alloy), free cutting, boron microalloyed, bearing and stainless steels for a wide range of application, including the automotive and construction industries.
Abrasive-type sawing unit for quality flats from Primetals Technologies. A comparable system will be installed in the bar rolling mill of Çemtaş in Bursa, Turkey.
This press release and a press photo are available at
Follow us on Twitter: twitter.com/primetals
Primetals Technologies, Limited, headquartered in London, United Kingdom, is a pioneer and world leader in the fields of engineering, plant building, and the provision of lifecycle services for the metals industry. The company offers a complete technology, product, and services portfolio that includes integrated electrics and automation, digitalization, and environmental solutions. This covers every step of the iron and steel production chain—from the raw materials to the finished product—and includes the latest rolling solutions for the nonferrous metals sector. Primetals Technologies is a joint venture of Mitsubishi Heavy Industries and partners, with around 7,000 employees worldwide. To learn more about Primetals Technologies, visit the company website www.primetals.com.