News & Press Releases
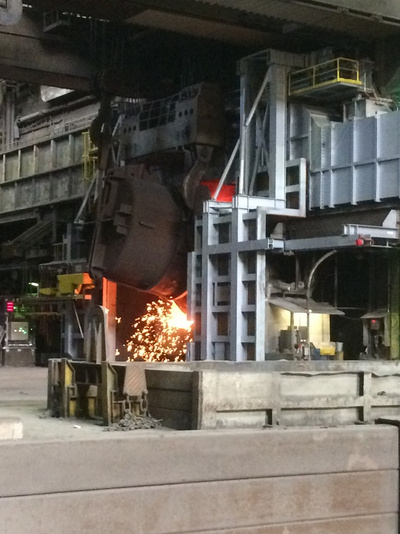
London, February 13, 2018
New LD(BOF) converter from Primetals Technologies enters service at ArcelorMittal Hochfeld
- Maintenance-free Vaicon Link 2.0 converter suspension offers long service life
- Newly developed horizontal measuring and sampling unit in use
At the end of January, a new LD(BOF) converter constructed by Primetals Technologies in a turnkey project entered service at the German steel producer ArcelorMittal Hochfeld GmbH. It has a tapping weight of 150 metric tons and replaces the previous "K2" converter. The converter is suspended by means of the maintenance-free Vaicon Link 2.0. This flexible and rugged suspension system ensures smooth load-bearing and compensates for heat-related deformations. A newly developed device for horizontal measuring and sampling from the tilted converter has also been installed. Primetals Technologies had received the order in mid-2016.
Primetals Technologies supplied the converter vessel, trunnion ring, suspension, slag protection and dog house gates. The scope of supply also included the horizontal measuring and sampling device, control desks and control stations, as well as technological control systems for a horizontal sublance. The converter has been made from highly heat-resistant materials to limit heat-related deformation. The maintenance-free Vaicon Link 2.0 converter suspension is designed so that deformations do not impair the movement of the converter. The automated probe manipulator for measuring temperature and CELOX as well as for taking samples from the tilted converter is a new development from Primetals Technologies and an attractive alternative to conventional technologies in terms of safety and measurement evaluation.
The project was implemented by a consortium led by Primetals Technologies in partnership with Buchinger Anlagen-Stahl-Rohrbau GmbH, a company based in Aurach am Hongar, Austria. Primetals Technologies was responsible for engineering and supplying the new plant components, the assembly engineering, supervision of the dismantling and assembly work and the cold test, as well as commissioning and training of the operating and maintenance personnel. Buchinger handled the dismantling of those old plant components for which there is no further use, and the assembly of the new plant components.
Ruhrort is one of two sites operated by ArcelorMittal in Duisburg and produced around 1.2 million metric tons of crude steel in 2016. The steel produced in the oxygen furnace plant is cast by two continuous casters. Some of the production output is shipped directly to ArcelorMittal's customers, but most of it is either processed in the billet mill or sent as input material to the wire mill at Hochfeld, the second Duisburg site. Here the billets are processed to form high-quality wire rods with diameters ranging from 5.5 to 25 millimeters.
LD(BOF) converter from Primetals Technologies at ArcelorMittal Hochfeld in Germany
Primetals Technologies, Limited, headquartered in London, United Kingdom, is a pioneer and world leader in the fields of engineering, plant building, and the provision of lifecycle services for the metals industry. The company offers a complete technology, product, and services portfolio that includes integrated electrics and automation, digitalization, and environmental solutions. This covers every step of the iron and steel production chain—from the raw materials to the finished product—and includes the latest rolling solutions for the nonferrous metals sector. Primetals Technologies is a joint venture of Mitsubishi Heavy Industries and partners, with around 7,000 employees worldwide. To learn more about Primetals Technologies, visit the company website www.primetals.com.