COUPLED PICKLING LINE & TANDEM COLD MILL
Achieves high-capacity production of high-quality products.
For a wide range of product applications, the required strip thickness, flatness, and surface quality can be achieved more economically by linking the pickling and cold-rolling processes. This offers significant improvements with respect to mill productivity, overall yield, and production cost savings as a result of the elimination of strip-threading and tailing-out operations. Speed-optimization systems from Primetals Technologies ensure the highest throughput rates under all operating conditions. In addition, maintenance, roll consumption, and manpower requirements are lowered. Typical production capacities of this type of combined facility are in the range of 1.2–2 million t/a.
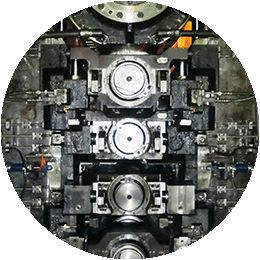
Market-Leading and Proven Technology
The coupled pickling line and tandem cold mill (PL-TCM) using Universal Crown Control Mill (UC-MILL) has become a de facto standard for large-scale prodcution of high-quality strip.
Main benefits:
- Highest production rates (1.2-2 million t/a) with optimized yield
- Tight tolerances for strip thickness and flatness with uniform high-quality surface
- Easy maintenance and minimum down times
- Stable operation
Technical features:
- i Box pickling tank - advanced pickling tank with high performace and minimal acid consumption
- 6-high UC-MILL with smaller work roll diameter and intermediate-roll shifting method delivers high reduction and excellent flatness control
- HYROP-F (Hydraulic Roll Position Control System with Force Motor Valve) as high response HAGC system
- Multi-zone work roll cooling ensures excellent shape control to achieve tight tolerances right from the start
- Flexible thread-in and thread-out strategies for all kinds of materials
- Last stand can be used for smoothing or texturing strip surface
- Minimize downtime for roll change with fully automated work roll and intermediate roll
- High speed rotary shear allows continuous operation of tension reel without stoppage at coil switchover
- Carrousel tension reel achieves stable coiling of lead-end and tail-end
- Fully automatic operation enables operators to focus on product quality, and intervention is reduced to an absolute minimum
- Precise trimming with FWC (Flying Width Changing) side trimmer
- Edge-drop control by work roll shifting device is reccomened in particular for elecrical sheet product
Want to know more? Go to Lifecycle Services & Integrated Plants & Solutions
Complete automation and process control for Coupled Pickling Lines and Tandem Cold Mills
Plant productivity and product quality are substantially depending on the quality of plant automation, process control, and available process optimization functions. To get the best performance out of a plant, Primetals Technologies provides add-on specific optimization solutions for further improvement of production efficiency and strip quality, besides standardized high performance automation system.
Throughput maximization with:
- Off Gauge Optimizer for integrated rolling process
- Speed Optimization System for throughput optimization
Excellent strip quality with:
- Pickling Optimizer : Advanced Pickling Model for highest pickling performance
- Roll Eccentricity Expert for uniform and accurate strip thickness
- Coil Eccentricity Expert for uniform and accurate strip thickness
- Flatness Expert: Model based Automatic Flatness control
- ChatterMon / Mill Chatter Monitoring with automatic process speed adaptation
Production flexibility and special steel grades:
- Precise mill setup by high-sophisticated rolling models complying with changing production requirements and high strength steel qualities
- Neural network based adaptation and setups promising high product flexibility and easy extension of the production to new materials
- Optimized weld seam rolling supporting flexible production and obtaining minimum off-gauge
TECHNOLOGY AND MODERNIZATION PACKAGES
Get striking results with incremental investments
Name | Short Description |
---|
Name | Short Description |
---|
Name | Short Description |
---|
Name | Short Description |
---|---|
PL-TCM Coupling | Couple CPL and TCM processes in one line |
Upgrade to HYPER UC-MILL | Upgrade conventional mill to Hyper UC-MILL with minimal modification |
Pickling Optimizer | Automated model-based setup calculation for efficient strip pickling |
TorqueMon | Inline measurement of roll spindle torque for rolling mills |
EdgeMon | Inspection of side-trimmed strip edge surface for steel pickling and processing lines and aluminum rolling |
Air Bearing Shapemeter | Shape measurement of rolled metal sheet and foil |
Position Transducer | Position measurement of rolling mill hydraulic capsule |
Additional UC-MILL stands | Additional UC-MILL stand installation for Tandem Cold Mill |
Work Roll Shift | Taper work roll shifting for Tandem Cold Mill |
i Box Pickling Tank | Advanced solution for efficient descailing |
High-capacity tension scale breaker | Tension leveler-type scale breaker for high descaling performance |
Flying Width Changing (FWC) side trimmer | Innovative solution for efficient and accurate side trimming |
Modular Coil Shuttle System (MCS) | Rail-based, fully automated modular coil transport system |
Name | Short Description |
---|
Name | Short Description |
---|
Reference Story: Best solution to efficiently produce high strength steel for automotive panel
Customer:
Severstal Dearborn (AK Steel since 2014), North America
Type of Plant:
Pickling Line and Tandem Cold Mill for carbon steel production including HSS
Technical data:
Strip Thickness: 0.37(0.30) ~ 2.67 mm
Strip Width: 736 mm~1,830 mm
Mill Type: 6-high UC-MILL (No.1 to 5 Stand)
Our solution:
This marked the first PL-TCM supplied in the U.S.A. by Primetals Technologies, the equipment configuration is optimized for automotive panel production.
i Box pickling tank:excellent processability for ultra-low carbon steel and high-tensile steel.
6 feet 5-stand UC-MILL: produces wide strip for automotive panel.
In-line inspection : surface inspection can be done right after rolling to minimize time needed to detect surface defect, unlike the conventional off-line inspection.