STECKEL & PLATE STECKEL MILLS — SPECIALIZED SOLUTIONS BASED ON ENGINEERING EXPERIENCE
Flexible configurations, meeting specialist needs, and adapting to changing market conditions for high-value coil and plate production.
Steckel Mills, thanks to low capital investment costs, occupy a special niche in hot flat rolling. They operate at a lower economic volume than hot strip mills but are capable of greater widths and are especially suitable for niche products and stainless steels. Capable of rolling strip and plate in a single mill line, the Plate Steckel Mill offers the ultimate flexibility to respond to market demands. Delivering high utilization and yields on plate products and producing wide coil products outside the range of Hot Strip Mills. Both are complex processes that Primetals Technologies has mastered.
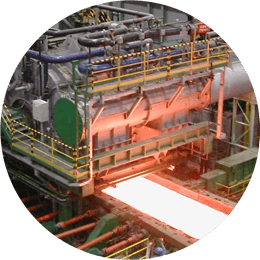
STECKEL MILLS FOR LOW COST AND HIGH QUALITY
A Steckel Mill is a reversing mill stand equipped with entry and exit coiler furnaces. Roughing Mills, Edgers and additional finishing stands can be added depending on specific customer needs.
A typical Steckel Mill line consists of:
- Reheating Furnace
- Primary Descaler
- Roughing Mill Stand with attached Edger
- Rotary Crop Shear
- Steckel Mill Stand with entry and exit Coiler Furnaces
- Laminar Cooling System (with option for high flow or Direct Quenching Section)
- Downcoiler
Primetals Technologies has developed several unique features to improve operation, product quality and production efficiency including:
Passive Deflector Roll
Each coiler furnace is equipped with a passive deflector roll to reduce tension variation in the strip, leading to improved rolling stability.
Closed Bottom Coiler Furnace with 2-stage guide
A patented 2-stage guide directs the strip onto the coiler furnace drum slot and also closes the bottom of the furnace, improving heating efficiency and uniformity.
Mill Stabilizing Device (MSD)
The special design of the MSD for Steckel Mill Stand can significantly suppress vibration at strip threading and tail-out during reverse rolling, helping to improve strip steering.
Power Coiler
The market demand for thicker and high strength products is met by the Power Coiler. This Downcoiler uses 4 Wrapper Rolls to help form the coil, ensuring tight wraps and high quality coils across the full hot rolled product range, including the highest strength pipeline steels.
Plate Steckel Mills for flexibility and functionality
A Plate Steckel Mill is essentially a wide Steckel Mill with a Plate Mill finishing line added. The plates are processed by a Hot Leveller after the downcoiler, leading into cooling beds and a shear line. A key difference is the position of the Rotary Crop Shear (RCS) after the Plate Steckel Mill stand, as opposed to the entry side on a conventional Steckel line.
The Rotary Crop Shear on the exit side of the mill stand allows plates to be cut from the coil on the final pass. To maximise production rates these 'intermediate plates' should be as large as possible and cut to final size in the shearline. When products are too thick to be coiled, they are produced as discrete plates, like a conventional Plate Mill.
Want to know more? Go to Lifecycle Services & Integrated Plants & Solutions
COMPLETE AUTOMATION AND PROCESS CONTROL FOR STECKEL MILLS
Plant productivity and product quality are substantially depending on the quality of plant automation, process control, and available process optimization functions. Primetals Technologies provides standardized high-performance automation systems seamlessly integrating:
- Digitalization packages (e.g. TPO, MAT, Condition Monitoring, Intelligent Sensors)
- Production management systems (Level3)
- Physical models combined with artificial intelligence (Level 2)
- Automation solutions including advanced technological controls (Level1)
For existing installations optimization packages are available as stand-alone solutions to improve production efficiency and strip quality.
Throughput maximization with:
- Dynamic Batching and advanced Interleaving for thermo-mechanical rolling
- Mill Pacing including Cooling beds charging optimization
Excellent strip quality with:
- Contour and Flatness Optimizer
- Model predicted roll alignment control to minimize camber (MRAC)
- Wedge and Camber Expert
- De-Tappering to improve Head/Tail thickness tolerances
Our solutions provide:
- Process Automation Twin to safely develop new materials and to optimize rolling schedules
- Central Operation Cockpit to support mill operations (centralized pulpit)
- Software architecture open for customers own future developments
- Modular structure for step-by-step modernizations
TECHNOLOGY AND MODERNIZATION PACKAGES
Get striking results with incremental investments
Name | Short Description |
---|
Name | Short Description |
---|
Name | Short Description |
---|
Name | Short Description |
---|
Name | Short Description |
---|
Name | Short Description |
---|
Name | Short Description |
---|