HOT METAL TREATMENT — CONTROL HOT METAL ANALYSIS TO ENSURE HIGHEST STEEL CLEANLINESS
Primetals Technologies offers all technologies and solutions for hot metal treatment to ensure constant low levels of steel impurities, like S, P to meet strictest quality requirements.
In order to maximize converter productivity and limit downstream refining costs, it is important to carefully prepare hot metal prior to the steelmaking phase. The solutions offered by Primetals Technologies include Sulfur removal, Silicon removal, Phosphor removal, and other specialized processes to reduce contents of Vanadium, Chromium, Titanium, and Manganese.
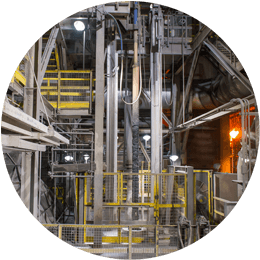
Hot Metal Treatment
Steelmakers are nowadays facing the challenge that quality requirements for their final products are increasing while quality of the raw material input is decreasing. For example, fracture toughness of steel continuously increased over the last decades by decreasing the limits for Sulfur and Phosphor content in the steel. On the other hand, processing of iron ore with higher Phosphor levels brings significant economic benefits due to the low price of such ore compared to high quality ore low in Phosphor; same can be said for coal high in Sulfur.
To master these challenges hot metal treatment processes have been developed. Principle idea is to remove unwanted elements from the hot metal in a separate process step before the hot metal is charged to the converter. Most important in this respect is the removal of Phosphor and Sulfur, minor topics are Vanadium and Titanium. Hot metal treatment allows further to split the complete steelmaking process in separate process steps which are rather simple and easier to control, making steel production process more robust.
Within the last years Primetals Technologies continuously developed and improved its solutions and has now a full portfolio for hot metal treatment. For example for Sulfur removal solutions for treatment in the torpedo car, Sulfur removal in the ladle via mono or co-injection as well as mechanical mixing with stirrer in KR process can be offered. For Phosphor removal treatment solutions in converter or ladle have been developed and successfully implemented in several plants.
Want to know more? Go to Integrated Plants & Solutions
Basic automation and Process optimization
Thus it enables cost savings and maximum flexibility under consideration of the individual hot metal conditions, target steel requirements and production situation.
Basic automation
Together with failsafe equipment, the powerful control system provides highest safety levels. The use of well-proven sensors and operating elements enables a smooth, reliable and automatic desulfurization process. All important signals are collected and monitored via our new HMI system, thus supporting a simple and systematic operation.
Process optimization
Intelligent control of the desulfurization process is performed by the application of dynamic process models. The prediction model provides a forecast of the entire process and predicts the required desulfurization reagent amounts, flow rates, the optimum ratio between injection materials as well as the optimum type of injection. The online supervision models cyclically monitor the actual process, calculating the actual condition (weight, analysis and temperature) of hot metal and slag. If during the process an actual sulfur content of hot metal is received from the laboratory, a new calculation is immediately started in order to update the ongoing treatment and new target setpoint values are defined.
ECO Solutions for hot metal treatment — Saving resources, creating value
Please follow the corresponding links to learn more about our competences.
Gas Cleaning
ECO Consulting
TECHNOLOGY AND MODERNIZATION PACKAGES
Get striking results with incremental investments
Name | Short Description |
---|
Name | Short Description |
---|
Name | Short Description |
---|
Name | Short Description |
---|
Name | Short Description |
---|
Name | Short Description |
---|