News & Press Releases
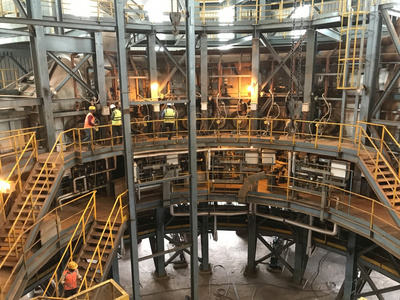
London, October 30, 2020
World´s first Circular Pelletizing Plant from Primetals Technologies started-up at Pro Minerals in India
- World´s most compact pelletizing plant
- Production capacity of 1.0 million tons of pellets per year
- Combines well-proven travelling grate process with circular dip-rail cooler
- Highly efficient use of equipment, low operational expenses and zero waste
- Fully automated process control and operation
In October, the world´s most compact pelletizing plant was started-up at the Basantpur, Keonjhar district site of Pro Minerals Pvt. Ltd. (Pro Minerals) in the Indian State of Odisha. The plant was supplied by Primetals Technologies and applies Circular Pelletizing Technology (CPT). The plant is designed to produce pellets suitable for coal-based direct-reduction (DR) production at a capacity of 1.0 million tons per year. CPT combines the well-proven travelling-grate process with the simple, compact and robust mechanical design of a circular dip-rail cooler. The result is a pelletizing technology with small footprint and low space requirements. CPT plants provide a highly efficient use of equipment, low operational expenses, zero waste and fully automated process control and operation, thus offering a number of advantages over conventional pelletizing plants.
Pro Minerals, was acquired by Essel Mining & Industries Limited, an Aditya Birla Group company in 2019. Aditya Birla Group is a US$ 48 Billion Global Diversified conglomerate, is in league of Fortune 500, with presence spanning across 36 countries. The CPT plant is located amidst mineral rich Barbil-Barajamada belt in the State of Odisha.
The pelletizing plant´s active induration furnace area amounts to 191 m2. Primetals Technologies scope of supplies and services included the design of the induration furnace and the design of the preprocess facilities, like additive grinding, mixing and green pelletizing, as well as advisory and start-up services.
Circular Pelletizing Technology
The ever-higher portion of fine and ultrafine iron ore from mining sites means that the pelletizing process is becoming more important for ore agglomeration. This has led to an increased interest by steel producers to invest in their own pellet plants to become independent of changing prices for pellets on the global market. Up until now, however, space requirements and high investment costs for a conventional plant generally precluded its installation within an existing steel plant.
As an answer to this situation and simultaneously to reduce the capital expenditures for new facilities, Primetals Technologies developed Circular Pelletizing Technology (CPT). This solution is based on the well-proven travelling-grate pelletizing process; however, the circularly designed induration furnace greatly reduces the footprint of the pelletizing plant. Overall space requirements for CPT are comparably less than those needed for a conventional pellet plant. Costs for civil works, equipment and steel structure are reduced accordingly and plant installation can be completed far more quickly. The circular arrangement of the induration furnace also results in a more efficient utilization of high cost key equipment. Hence, only 50% of pallet cars are installed compared to a straight-type induration furnace of the same capacity. In addition, heavy equipment like lifting and lowering wheel which is typical for manipulation of pallet cars in straight-type plants is not required.
The intelligent and maximized reuse of hot gases minimizes the energy consumption required for pelletizing and, in combination with total recycling loops for waste materials and even steel mill reverts, a low environmental impact is ensured by the process. The installation of CPT within a steel plant not only allows producers to become independent of erratic prices for commercially available pellets, the chemistry and quality of the pellets can also be flexibly adjusted to meet the requirements of blast furnaces or direct-reduction plants. Primetals Technologies´ advanced automation system is an integral component of CPT which ensures optimized operational control for lowest fuel consumption and highest production capacity.
Circular Pelletizing Technology (CPT) plant from Primetals Technologies in operation at the Basantpur, Keonjhar district site of Pro Minerals Pvt. Ltd. (Pro Minerals) in the Indian State of Odisha
Primetals Technologies, Limited, headquartered in London, United Kingdom, is a pioneer and world leader in the fields of engineering, plant building, and the provision of lifecycle services for the metals industry. The company offers a complete technology, product, and services portfolio that includes integrated electrics and automation, digitalization, and environmental solutions. This covers every step of the iron and steel production chain—from the raw materials to the finished product—and includes the latest rolling solutions for the nonferrous metals sector. Primetals Technologies is a joint venture of Mitsubishi Heavy Industries and partners, with around 7,000 employees worldwide. To learn more about Primetals Technologies, visit the company website www.primetals.com.