News & Press Releases
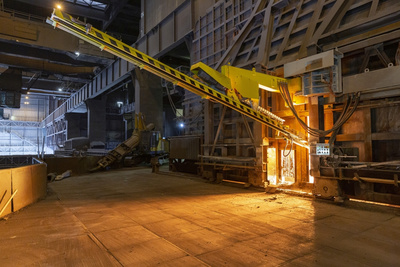
London, November 10, 2020
Successful Start-up and FAC for two semi-automatic horizontal temperature and sample-taking manipulator systems at converter steel plant in Dillingen, Germany
- Automated measurement/sample taking process, no manual handling of heavy lances
- Improved reproducibility of temperature measurements and sample taking
- Improved safety by minimized residence time of operator in front of doghouse door during measurements/sample taking
- Highest availability of 98% in three-shift operation
- Improved automation
Primetals Technologies has received the final acceptance certificate (FAC) for two semi-automatic horizontal temperature and sample-taking manipulator systems installed at the two BOF converters at the steel plant of Dillinger Hütte (AG der Dillinger Hüttenwerke) in Germany. The aims of this modernization project were to improve operational safety by automating the processes and thus reducing physical presence of operators in potentially hazardous environment as well as to improve availability – up to 98% in three-shift operation and reproducibility of temperature measurements and sample taking. Previously, temperature measurement and sample taking at the two 190-ton-converters were conducted manually.
With the new systems, measurement and sample taking processes can take place while the doghouse doors are closed via a newly installed fully automated opening/closing flap. It is also possible to parallelly measure temperature and take samples within one operation/measurement step. The position of the sampling/measurement process in the converter is highly reproducible at maximum charging weight of approximately 210 tons and minimum charging weight of approximately 150 tons, within the converter tipping angles from 83° up to 95°. The measuring lance may be exchanged in less than 10 minutes by two employees during normal converter operation. The exchange of the complete manipulator system at the doghouse door, including disassembly and assembly, mechanics, electrics and media can be performed within one shift (under 9 hours) by quick changing devices and connections.
The residence time of the measuring lance inside the converter is minimized to below 25 seconds, including time for measuring itself, to minimize the heat load of the lance and maximizing its lifetime. Temperature measurement was integrated in the existing temperature analysis system. The manipulator systems are conceived as a low-maintenance design, e.g. by newly developed quick coupling systems at the measuring lance. The existing doghouse doors remained fully functional after manipulator installation. Usage of existing doghouse doors including drives required no modifications regarding statics or motor capacity due to the optimized weight distribution of the manipulator systems. The systems are fully CE compliant regarding design and the safety automation and operation concept within the existing converter steel plant.
Primetals Technologies was responsible for the project management, basic and detail engineering, manufacturing and preassembling, functional tests, packing and transport, erection for mechanics and electrics and automation, commissioning, training on the mechanic and electric equipment, and operation, test-operation with on-call duty, guarantee tests for two semi-automatic horizontal manipulator systems for temperature and oxygen activity measurements as well as steel and sludge sample-taking. Erection and commissioning were carried out during normal converter maintenance and operation. Erection works were finished within 4 days, cold commissioning was finished within 2 days, hot commissioning was finished within 3 days.
The Dillinger Group is made up of a series of top-ranking companies which together provide maximum quality and best possible service in the field of heavy plate. This applies both to the work of the integrated iron-and-steel plant, to the production of coke and smelting of iron by Zentralkokerei Saar GmbH and ROGESA Roheisengesellschaft Saar mbH, two subsidiaries owned jointly with Saarstahl AG, and to the production of liquid steel and semi-fabricates. Heavy plate is produced at two locations, Dillinger Hütte, in Dillingen, and Dillinger France, in Dunkirk.
Semi-automatic horizontal temperature and sample-taking manipulator systems installed at the converter steel plant of Dillinger Hütte in Germany by Primetals Technologies (Image courtesy Dillinger Hütte)
Primetals Technologies, Limited, headquartered in London, United Kingdom, is a pioneer and world leader in the fields of engineering, plant building, and the provision of lifecycle services for the metals industry. The company offers a complete technology, product, and services portfolio that includes integrated electrics and automation, digitalization, and environmental solutions. This covers every step of the iron and steel production chain—from the raw materials to the finished product—and includes the latest rolling solutions for the nonferrous metals sector. Primetals Technologies is a joint venture of Mitsubishi Heavy Industries and partners, with around 7,000 employees worldwide. To learn more about Primetals Technologies, visit the company website www.primetals.com.