News & Press Releases
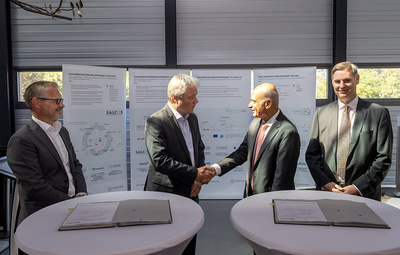
London, August 25, 2022
Salzgitter places large order with Primetals Technologies for electric arc furnace as part of major green steel transformation program
- Salzgitter AG orders Electric Arc Furnace Ultimate designed to produce 1.9 million tons of steel per year
- An important step toward long-term aim of green steel production
- Start of production planned for end of 2025
On August 23rd, German steel producer Salzgitter signed a contract with Primetals Technologies for an EAF Ultimate. With a tapping weight of 220 tons, the furnace will have an annual capacity of 1.9 million tons of steel. It will be implemented at the steel plant in Salzgitter, Germany. Startup is scheduled for end of 2025.
World’s largest green steel transformation program
Salzgitter is investing in the world’s leading transformation program in the steel sector. The Salzgitter Low CO2 Steelmaking (SALCOS) project aims to convert the existing integrated steel plant to green steel production in three stages by 2033. As part of the transformation, two direct reduction plants and three electric furnaces will be built, which will then successively replace the existing blast furnaces and converters. This order for one EAF with Primetals Technologies marks the first step in this process.
“It underscores our ambition to remain a leader in the decarbonization of the steel industry and to set up the Salzgitter site for the future on a lasting basis. With Primetals Technologies, we have a strong partner on our side – true to our strategy of moving toward a sustainable industry,” said Ulrich Grethe, Head of Steel Production at Salzgitter.
Several recent EAF references
Several factors played a role when Salzgitter choose Primetals Technologies as supplier. A sound reference base with several recent successful EAF projects, low consumption figures of the technologies involved, and competence in project management were three main factors. The scope of supply includes engineering, supply, and construction.
"Primetals Technologies is pleased to support Salzgitter AG's decarbonization projects with the installation of a highly efficient EAF. With our Green Steel technology, we enable low CO2 steel production,” said Aashish Gupta, Executive Vice President and Head of Upstream at Primetals Technologies.
Special features
EAF Ultimate is part of Primetals Technologies new generation of electric steelmaking equipment. It is characterized by short tap-to-tap times, fully automated operation, and advanced control systems. The Salzgitter EAF features dust removal systems, a heat recovery system, a water management system, electrical compensation for grid stabilization and material handling for alloying materials and additives. It will also include Level 1 and 2 automation and the LiquiRob robot system.
The heat recovery system will convert much of the waste heat into steam which is then fed back and used in other production units. Part of an extensive digitalization package, the condition-monitoring system ALEX will identify potential incidents before they occur. The tailormade Lomas off-gas analysis system determines all relevant values of the off-gas composition to ensure higher availability, reduced energy consumption and increased safety measurements.
Massive CO2 emission savings
The SALCOS project will replace a coking-coal-based steelmaking process with a new hydrogen-based route. This is expected to save around 95 percent of the annual CO2 emissions of around 8 million tons. One of Germany's leading steel and technology groups, Salzgitter has an annual capacity of 7 million tons of crude steel. The group employs 25,000 people worldwide in 150 national and international subsidiaries and associated companies.
SALCOS is a registrered trademark of Salzgitter AG.
Representatives from Salzgitter and Primetals Technologies at the contract signing ceremony. From left to right: Alexander Stein, Managing Director at Salzgitter Flachstahl, Ulrich Grethe, Head of Steel Production at Salzgitter, Aashish Gupta, Executive Vice President at Primetals Technologies, and Dr. Jan Friedemann Plaul, Senior Vice President at Primetals Technologies.
Primetals Technologies, Limited, headquartered in London, United Kingdom, is a pioneer and world leader in the fields of engineering, plant building, and the provision of lifecycle services for the metals industry. The company offers a complete technology, product, and services portfolio that includes integrated electrics and automation, digitalization, and environmental solutions. This covers every step of the iron and steel production chain—from the raw materials to the finished product—and includes the latest rolling solutions for the nonferrous metals sector. Primetals Technologies is a joint venture of Mitsubishi Heavy Industries and partners, with around 7,000 employees worldwide. To learn more about Primetals Technologies, visit the company website www.primetals.com.