News & Press Releases
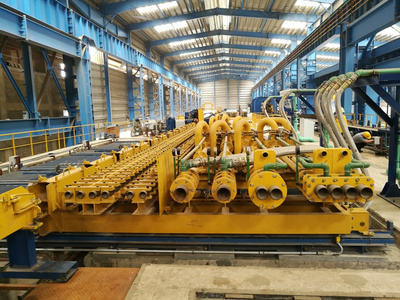
London, December 04, 2018
Primetals Technologies to supply billet caster and bar rolling line for minimill project of Naveena Steel, Pakistan
- Enables Naveena Steel to enter growing market for regional infrastructure projects
- Production capacity is 270,000 metric tons of rebars per year
- Smaller diameters are rolled in multi-slit mode to increase productivity
- Direct rolling of hot billets will reduce fuel cost
Primetals Technologies has received an order from Naveena Steel Mills (Private) Limited (Naveena Steel) to supply a continuous billet casting machine and a bar rolling mill for a new minimill in Port Qasim, Karachi. The billet caster will be supplied by Concast (India) Ltd., a Primetals Technologies group company. The new mill will enable Naveena Steel to the enter the growing market for regional infrastructure projects. The minimill will produce around 270,000 metric tons of reinforcing steel (rebars) per annum with diameters ranging from 8 to 40 millimeters. Diameters up to 12 millimeters will be rolled in multi-slit mode to improve productivity. As a special feature of the new plant, billets will be directly charged in hot condition to the rolling mill, which will provide significant energy savings. An inline induction furnace placed before the first rolling stand will serve to equalize the billet temperature, providing the seamless integration of the caster and rolling processes. Commissioning is scheduled to start in the second quarter of 2019.
Naveena Steel was founded in 2018. It is part of the family-owned Naveena Group. Established in 1971, it is active in the textile, wind-power and real-estate areas. Current production sites are in Karachi, Lahore, Pakistan and Dubai, UAE. In the context of the implementation of the China Pakistan Economic Corridor project in Pakistan, infrastructure development is expected to increase steel demand. For this reason, Naveena Steel is planning to set up facilities for melting, casting and rolling with a total capacity of 270,000 metric tons per year. The minimill will be located in proximity to Port Qasim, Karachi, resulting in cost effective import of basic raw materials like scrap.
The continuous casting machine consists of two strands, with provisions made to add a third strand in the future. The caster has a curved tube mold, and is a multiple-radius machine, with a basic radius of 6 meters and a second radius of 11 meters. Maximum casting speed is 4 meters per minute. Concast (India) is responsible for designing, engineering and manufacturing of ladle support, tundish and tundish support, mold and oscillator, straightener segments, secondary cooling, dummy bar system as well as pusher and cooling bed. Concast (India) will also supply the basic automation (level 1) and HMI system. The caster produces the starting material for the bar rolling mill, 9 meter long billets of low and medium carbon steels, with a square cross-sections of 130 x 130 millimeters.
The billets will be hot charged to the rolling mill, which will produce rebars with diameters ranging from 8 to 40 millimeters. In order to increase the productivity of the plant, bars with diameters between 10 and 12 millimeters will be rolled in two-slit mode, and those with diameter 8 millimeters in three-slit mode. The rolling line will consist of a furnace discharging area, a 6-stand roughing mill in VHVHHV arrangement, a 6-stand intermediate train in HVHVHV arrangement, and a 4-stand finishing train in HHHH arrangement. The type of all rolling stands will be Red Ring Series 5. The maximum rolling rate is 45 tons per hour, the maximum finishing rolling speed amounts to 12 meters per second.
An inline PQS quenching system gives the bars a tempered martensitic case and a ferritic-pearlitic core, enabling Naveena Steel to obtain the YTS UTS A% values required by applicable standards (like DIN, ASTM, and Indian standards). The downstream hot dividing shear is equipped with an optimization system to maximize the utilization of the cooling bed and guarantee the pre-set number of commercial-length bar layers per bundle. The cooling bed is 54 meters long and 8 meters wide, with the possibility to extend it in future to a total length of 66 meters. A cold static dividing shear, handles the final cutting of the rolled bars. This is followed by automatic bundling, binding, weighing and dispatching of bundles. The scope of supply also includes fluid systems and operational parts, such as stand-by Red Ring stands, rolling rolls and guides.
Primetals Technologies will also supply HMI hardware and system software, control desks, the basic (level 1) automation, as well as motors and drives for the rolling mill. In addition, Primetals Technologies will deliver services for erection, commissioning and training.
The inline PQS quenching system from Primetals Technologies gives bars a tempered martensitic case and a ferritic-pearlitic core. The PQS is part of Primetals Technologies´ supply of a continuous billet caster and a rebar rolling mill for the minimill project of Naveena Steel in Pakistan.
Primetals Technologies, Limited, headquartered in London, United Kingdom, is a pioneer and world leader in the fields of engineering, plant building, and the provision of lifecycle services for the metals industry. The company offers a complete technology, product, and services portfolio that includes integrated electrics and automation, digitalization, and environmental solutions. This covers every step of the iron and steel production chain—from the raw materials to the finished product—and includes the latest rolling solutions for the nonferrous metals sector. Primetals Technologies is a joint venture of Mitsubishi Heavy Industries and partners, with around 7,000 employees worldwide. To learn more about Primetals Technologies, visit the company website www.primetals.com.