News & Press Releases
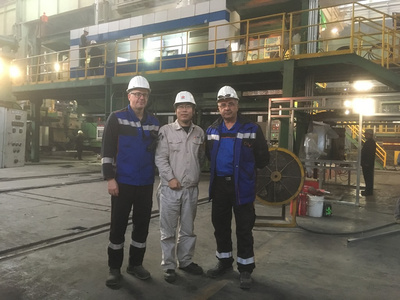
London, February 26, 2019
Primetals Technologies receives final acceptance for modernized continuous slab caster at Angang Iron & Steel
- Modernization improves productivity and product quality
- Greater flexibility for product mix and casting formats
- Casting machine was revamped within just 30 days
- Fast project implementation minimized downtimes
- 1,700 heats equaling approximately 348,000 tons processed from start-up to FAC
In December 2018, Primetals Technologies received the Final acceptance Certificate (FAC) for the modernized two-strand continuous slab caster CCM1 in steel works no. 3 of Angang Iron & Steel Group Co. in Anshan, China. The caster was started-up in late October 2018 and processed more than 1,700 heats equaling approximately 348,000 tons within less than two months. The objectives of the project were to improve the product quality and productivity, and also to increase the flexibility of the processing of different steel grades and casting formats. The casting plant is equipped with modern equipment and technology packages, including DynaGap Soft Reduction to improve the interior quality of the slabs. In order to minimize shutdown times, the project planning attached particular importance to a quick implementation: the casting machine was revamped within just 30 days.
Angang Iron & Steel Group Co. is located in Anshan in Liaoning Province. It has an annual production of approximately 35.8 million metric tons (2017), and is one of China's leading steel producers. Steel works no. 3 in Anshan employs a conversion route through a basic oxygen converter, ladle furnace and RH plant. It has an annual capacity of five million metric tons and supplies two casting plants. Continuous slab caster CCM2 has already been modernized by Primetals Technologies and has been back in successful operation since July 2015.
The two-strand continuous slab caster CCM1 in steel works no. 3 has a production capacity of 2.5 million metric tons per annum. Its machine radius is nine meters and metallurgical length 36 meters. The caster produces slabs with a thickness of 230 millimeters in widths ranging from 990 to 1,550 millimeters. The maximum casting speed is 2.1 meters per minute. The plant casts ultra-low carbon to high carbon steels, peritectic, deep drawn and HSLA steels, as well as micro-alloyed, low-alloyed and silicon steels.
The modernization project included equipping continuous slab caster CCM1 with a new tundish car and a new tundish with LevCon mold level control. The straight cassette-type Smart Mold is equipped with the Mold Expert breakout detection system, DynaWidth for automatic width adjustment, and the DynaFlex mold oscillator. Bender and Smart Segments as well as I-Star rollers are used in the strand-guiding system.
The Dynacs secondary cooling system dynamically calculates and controls the temperature profile along the entire strand. This enables the working points of the strand cooling, and thus the final strand solidification, to be determined precisely as a function of the casting speed, slab format and steel grade. DynaGap Soft Reduction is used to improve the interior quality of the slabs. The roll gap is dynamically adjusted during the final solidification in accordance with the operating points calculated by Dynacs. This minimizes segregation in the center of the strand. The secondary cooling uses DynaJet spray cooling with a center/margin setting.
In addition, Primetals Technologies handled the basic engineering of the tundish, the ladle shroud, the dummy bar system, the supporting structure and the maintenance stands, as well as the detailed engineering for the shroud manipulator, the tundish car, mold and mold oscillator, the segments of the strand-guiding system, the secondary cooling and the dummy bar. The automation system and the consulting services for the construction and commissioning were also part of the order.
Primetals Technologies site manager Olaf Schwarze, Zhang Yong, director of steelmaking plant no 3., and Primetals Technologies commissioning manager Novica Mitic and (from left to right) in steelmaking plant no. 3 of Angang Iron & Steel Group Co. in Anshan, China.
Primetals Technologies, Limited, headquartered in London, United Kingdom, is a pioneer and world leader in the fields of engineering, plant building, and the provision of lifecycle services for the metals industry. The company offers a complete technology, product, and services portfolio that includes integrated electrics and automation, digitalization, and environmental solutions. This covers every step of the iron and steel production chain—from the raw materials to the finished product—and includes the latest rolling solutions for the nonferrous metals sector. Primetals Technologies is a joint venture of Mitsubishi Heavy Industries and partners, with around 7,000 employees worldwide. To learn more about Primetals Technologies, visit the company website www.primetals.com.