Digital Unity
Synchronize your production to achieve the full potential of your steel factory
Smart sensors, automatic functions and cyber-physical systems digitize your plant. Connectivity of plant equipment and data-based assistance of the workforce’s day-to-day agendas are essential factors shaping the future of metals production. Digital Unity is a digitalization-driven concept that integrates data from three key processes: production, quality, and maintenance. It consists of three digital software services: Production Management System (PMS), Through-Process Optimization (TPO), and Maintenance Asset Technology (MAT).
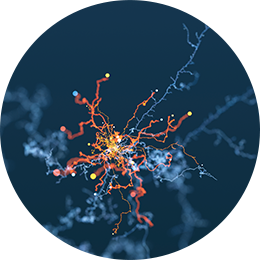
PRODUCTION MANAGEMENT SYSTEM (PMS) — INTEGRATION OF YOUR BUSINESS PROCESSES
The Production Management System (PMS) enables metals producers to attain horizontal and vertical integration of their complete business processes. It contains a complete set of modules covering various planning processes, such as:
- Demand and sales
- Flow and order
- Order and line scheduling
- Material planning
Production order lifecycle management, including order generation, order combination, and fulfillment tracking, goes hand in hand with schedule execution management to monitor and control all production activities. Embedded product disposition, deviation management, and through-process quality control determine the detailed quality status and allow you to manage any product defect. Logistics finally completes the system to optimize all material transport and inventory.
Dynamically plans and tracks your production to optimize all facilities during every step of the production process. Customer orders can be transformed into individual process instructions along the entire production route, applying extensive metals-specific application knowledge. The PMS optimizes productivity, ensures maximum flexibility to your customers’ requests, and safeguards product quality.
Our production-management solution is based on PSImetals, a comprehensive software suite that provides modules explicitly tailored to the metals industry. It is a system that has already proven its merits in numerous steel-production plants worldwide. PMS is a highly configurable solution that supports customers operating their production plant as an industry 4.0 "smart factory.
Through-Process Optimization (TPO) — INTERCONNECTED OPERATIONAL EXCELLENCE
Through-Process Optimization (TPO), provided by Primetals Technologies, is the interconnected solution that complements the steel production chain and advances IT platform functionality, creating the ultimate business advantage. TPO allows know-how embedded monitoring and the control of the process and product quality to improve and speed up communication and information exchange.
Through-Process Quality Control (TPQC) and smart services are two independent parts of TPO that complement each other perfectly. TPO is metals production for a new generation.
Think Big, Start Small
Improve performance, efficiency, and quality across all your plants – from the liquid phase to the finishing lines. With TPO being a highly scalable solution, it can flexibly adapt to your requirements. The number of functions, the number of production units you want to integrate into TPO, and the range of services are tailored to meet your specific needs.
- Data: Collect and visualize comprehensive quality data
- TPQC: Integrated know-how-based quality control system
- Services: Full range of services including know-how transfer
Advantages
- Increased profit and growth
- More efficient plant performance
- Production chain transparency and traceability
- Real-time decision support from production data
- Return on investment in less than one year
Read more about TPO in Process & Technology Consulting.
Maintenance Asset Technology (MAT) — TAKING MAINTENANCE TO THE NEXT LEVEL
Steel producers who wish to increase efficiency, productivity, and profitability, while improving maintenance quality and maturity may look toward MAT to support the management and execution of maintenance efforts in an entirely new way and unleash the full potential of a steel plant.
As a cornerstone of the Digital Unity from Primetals Technologies, MAT centralizes all maintenance activities by seamlessly interfacing with multiple software systems specially designed for the metals industry.
While highly customizable, MAT also comes with pre-configured metals know-how and is packed with all the essential features, from critical assessments and maintenance strategies for specific equipment to procedures, documentation, and checklists for responding to particular alarms.
Utilize the full potential of your assets with the features and benefits of MAT:
- Asset tracking: Instant access to component part histories
- Advanced scheduling: Assign work orders, manage human resources and equipment
- Work order tracking: Graphical support tool for tracking work order progress
- KPI dashboard: Automatic report generation supports data-driven decisions
- Portability: Runs on tablets for on-site and offline use
- Metals know-how: Maintenance know-how tailored to the metals industry
Reference Story: First Through-Process Optimization Project in China
Customer
Tangshan Iron & Steel (HBIS Group), China
Type of project
Supply of Through-Process Optimization package covering all process units from steel plant to annealing and galvanizing lines
Our solution
With the order for a new cold rolling complex at Tangshan, Primetals Technologies provided a TPO package to ensure the efficient production of AHSS and high-quality steel grades. The newly developed TPQC system was installed at the upstream facilities (steelmaking and hot rolling) and at the new CRM complex, which compromises a PLTCM, CAL, and three continuous galvanizing Lines. The experts of Primetals Technologies implemented intelligent rules, key performance indicators, and statistical process control to ensure the production of the best quality products. In addition, numerous training sessions for quality management, maintenance management, product development, and daily management have been provided.