News and Press Releases
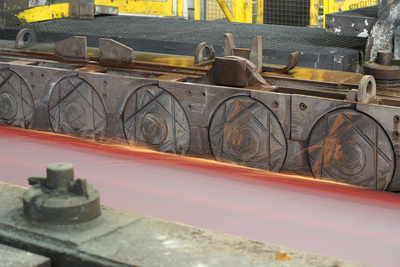
London, 09 February 2017
ArcelorMittal Eisenhüttenstadt orders Eco Slide Discs from Primetals Technologies as strip side guides for coiler
- Eco Slide Discs can be used for up to several months instead of just a few days
- Their inherent self-cleaning effect can reduce the risk of material deposits falling onto the strip and damaging its surface
- They eliminate maintenance activities and time-consuming welding and grinding repair work
- Major savings can be made on wear parts
Primetals Technologies has received an order from ArcelorMittal Eisenhüttenstadt, a German steel producer, to install Eco Slide Disc side guides on the entry side beams of a coiler in a hot-strip mill. They will replace the conventional wear plates. The reference plant at voestapline Stahl has shown that the rotatable discs can be used for up to several months, whereas the previous equipment lasted for only a few days. The new strip side guides have an inherent self-cleaning effect, which can reduce the risk of material deposits falling onto the strip and damaging its surface. The Eco Slide Discs are scheduled to be installed at ArcelorMittal Eisenhüttenstadt in July 2017.
ArcelorMittal is the world's largest steel producer and a worldwide supplier of high-quality steel products. At the company site in Eisenhüttenstadt, located in the German state of Brandenburg, the main products are high-quality, coated flat steels for the automotive industry, and steel products used for domestic appliances and the construction industry.
The strip entry side guides of the hot-strip mill coiler at ArcelorMittal Eisenhüttenstadt will be equipped with rotatable Eco Slide Discs mounted on maintenance-free, rugged side beams. The wear discs are mounted vertically between the table rollers and are automatically and synchronously rotated by a selectable angle after a variable number of strip sequences have passed. With conventional wear plates, the strip always cuts into the plate at the same point, whereas with Eco Slide Discs, the wear is
distributed evenly around the entire surface of the circular disc. This lengthens not only the service life of the wear parts but also lengthens the period of continuous operation of the entry side guides from the previous several days to several months. The periodic rotation of the discs means that only small amounts of material chafed from the strip edges can adhere to the discs, which are then removed during subsequent strip passage. The self-cleaning effect of the Eco Slide Discs eliminates the need for manual cleaning of the wear plates, which was previously required for certain strip qualities to prevent strip edge deposits from falling off and damaging the surface of the strip. Results from the voestalpine reference plant have so far shown that it is sufficient to turn over the Eco Slide Discs or replace them with new wear discs during a planned downtime for repairs after four to sixteen weeks of maintenance-free operation. The new discs eliminate the welding and grinding repair work that nearly all mill operators have to do on expensive wear plates.
Eco Slide Discs have been in successful use at the hot-strip mill of voestalpine Stahl in Linz, Austria since August 2014.
Side guides with Eco Slide Disc beams from Primetals Technologies at the entry side of the down coiler unit in the hot strip mill of voestalpine Stahl in Linz, Austria.
Primetals Technologies, Limited headquartered in London, United Kingdom is a worldwide leading engineering, plant-building and lifecycle services partner for the metals industry. The company offers a complete technology, product and service portfolio that includes integrated electrics, automation and environmental solutions. This covers every step of the iron and steel production chain, extending from the raw materials to the finished product – in addition to the latest rolling solutions for the nonferrous metals sector. Primetals Technologies is a joint venture of Mitsubishi Heavy Industries (MHI) and Siemens. Mitsubishi-Hitachi Metals Machinery (MHMM) - an MHI consolidated group company with equity participation by Hitachi, Ltd. and the IHI Corporation - holds a 51% stake and Siemens a 49% stake in the joint venture. The company employs around 7,000 employees.