REVERSING COLD MILL
Solution for small to medium-sized production capacities and special steel grades.
In Reversing Cold Mills, the tension reels are placed at both ends of a single or two-mill-stand arrangement. Because the rolling parameters can be quickly changed for each coil, Reversing Cold Mills are ideal for smaller-lot production of various product types, including high-grade silicon steel. The compact size and simple design allow easy access to equipment and machinery for maintenance purposes, and operation can be stopped and restarted more flexibly. The advanced features of Primetals Technologies’ Reversing Cold Mill with UC-MILL principle allow for stable operation and uncompromising quality of strip to meet strict tolerance requirements.
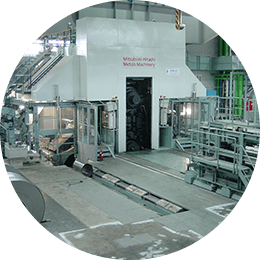
Variety of reliable mills based on UC-MILL principle
Single-stand Reversing Cold Mill
A single-stand cold rolling mill is capable of producing 100,000 to 400,000 t/a depending on product mix. Rolling schedules can be carried out with an even or odd number of passes to maximize mill availability and performance. UC-MILL with work roll bending, intermediate roll bending, intermediate roll shifting, and all-straight-roll applicaton ensures enhanced flatness control. Strip flatness measuring equipment mounted at one or both ends of the mill, combined with multi-zone work roll cooling, mean that the highest demands for flatness are met.
Two-stand Reversing Cold Mill
Primetals Technologies' two-stand Reversing Cold Mills combine the flexibility of single-stand reversing mills with the capacity of conventional coil-to-coil tandem mills at substantially reduced investment costs. Steel rolled in two-stand reversing cold mills is suitable for a wide range of applications, offering the best possible performance in terms of quality and productivity. A two-stand Reversing Cold Mill can deliver capacities of between 300,000 t/a of thin-gauge products or 1,000,000 t/a and more of thicker-gauge products.
Main benefits of Reversing Cold Mills
- High production capacity and yield
- Flexible, low-cost rolling of a wide range of products, especially for small order lots
- Tight strip thickness and shape tolerances
- Minimum off-gauge length
- High surface quality
- Second stand can serve as a skin pass mill
HYPER UC-MILL
The HYPER UC-MILL is a newly developed mill featuring even smaller work rolls to achieve high performance of strip gauge and flatness control for High Strength Steel (HSS) rolling. It is also applicable for production of high-grade, non-grain-oriented silicon steel and thin products.
Features:
- Smaller work rolls and optimized roll diameter combination with intermediate and back-up rolls
- Work roll-driven system for high flatness controllability
- Development of a high strength MH spindle for work roll drive
The optimized combination of roll diameters brings out the best performance of HYPER UC-MILL. In overall comparison, the HYPER UC-MILL’s work roll diameter is reduced by 20-30% from that of the standard UC-MILL to further reduce rolling force and the number of passes. MH Spindle is the fundamental technology to transmit the required torque for HYPER UC-MILL.
Want to know more? Go to Lifecycle Services & Integrated Plants & Solutions
Complete automation and process control for Reversing Cold Mills
Plant productivity and product quality are substantially depending on the quality of plant automation, process control, and available process optimization functions.
To get the best performance out of a plant, Primetals Technologies provides add-on specific optimization solutions for further improvement of production efficiency and strip quality, besides standardized high performance automation system.
Excellent Strip quality with:
- Roll Eccentricity Expert for uniform and accurate strip thickness
- Coil Eccentricity Expert for uniform and accurate strip thickness
- Flatness Optimizer - Model based Automatic Flatness control
- ChatterBlock Controller / Mill Chatter Monitoring with automatic process speed adaptation
For Reversing cold mills a highly optimized solution is available matching all kind of mill stand configurations. According to the complexity of production a look-up table or rolling model based mill setup can be chosen.
TECHNOLOGY AND MODERNIZATION PACKAGES
Get striking results with incremental investments
Name | Short Description |
---|---|
PL-TCM Coupling | Couple CPL and TCM processes in one line |
Modular Coil Shuttle System (MCS) | Rail-based, fully automated modular coil transport system |
Integrated Solenoid Valve (ISV) Spray System | ISV Roll coolant spray bars for hot and cold rolling mill strip flatness control |
Contactless Shape Monitor | Measuring strip flatness with no contact with the strip. |
Upgrade to HYPER UC-MILL | Upgrade conventional mill to Hyper UC-MILL with minimal modification |
TorqueMon | Inline measurement of roll spindle torque for rolling mills |
ALU TCS | Compact and integrated technological control system for single cold rolling mills |
Flatness Expert | Flatness control for tight shape tolerances |
Additional UC-MILL stands | Additional UC-MILL stand installation for Tandem Cold Mill |
Position Transducer | Position measurement of rolling mill hydraulic capsule |
Air Bearing Shapemeter | Shape measurement of rolled metal sheet and foil |
Reference Story: HYPER UC-MILL, the world's most efficient Reversing Cold Mill
Customer:
Maanshan Iron & Steel Co., China
Type of plant:
Reversing cold mill for silicon steel production
Technical data:
Mill type: HYPER UC-Mill
Strip thickness: 0.35 ~ 0.65 mm
Strip width: 900 mm ~ 1,280 mm
Our solution:
The installation of a Hyper UC-MILL enabled the customer to produce high-grade silicon products. The mill is capable of rolling thinner and harder materials, which had been impossible to accomplish with a conventional Reversing Cold Mill.